New £100k paper banding line saves an elephant’s worth of plastic going to landfill
A £100,000 investment means greetings printer Loxleys is saving over 6.2tonnes of plastic going into landfill each year by sending the cards it produces for publishers out wrapped in a paper band instead of plastic film.
The firm’s new fully-automated paper banding line creates an eco-band that’s a sustainable solution to transit packing, collating cards and envelopes in multiples of threes and sixes, replacing the need for traditional OPP plastic film.
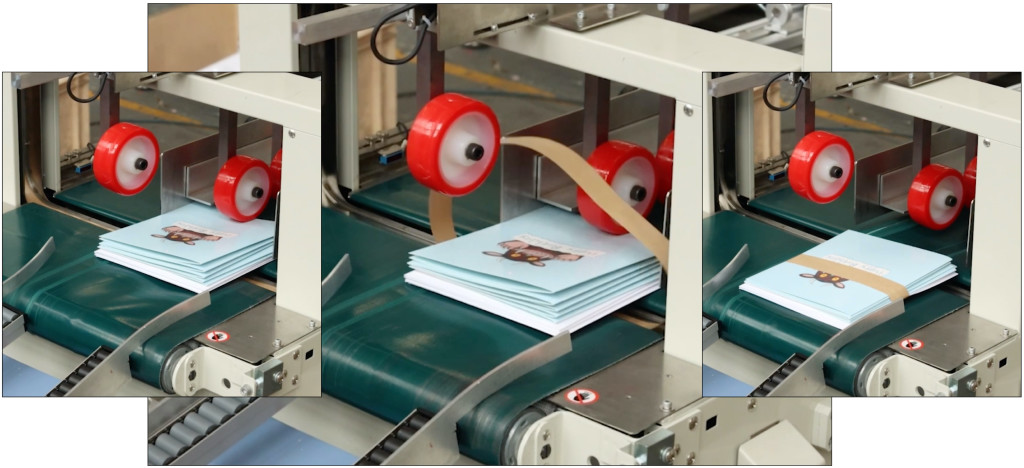
Loxleys’ md Tony Lorriman commented: “We are committed to minimising the environmental impact of a greeting card – our recent investments in new technology demonstrate this commitment by increasing the sustainability of our production process.”
The innovative new equipment is suitable for cards up to a maximum 9x6in size and has the capacity to gather and band 20million cards and envelopes per year, securing each set with a fully-recyclable paper band.
Tony said that, as a specialist manufacturer, Loxleys believes it is its responsibility to continuously develop eco-friendly alternative solutions and the investment in paper banding eliminates the use of plastic within the transit bagging process, offering publishers a more sustainable way to group and ship their cards.
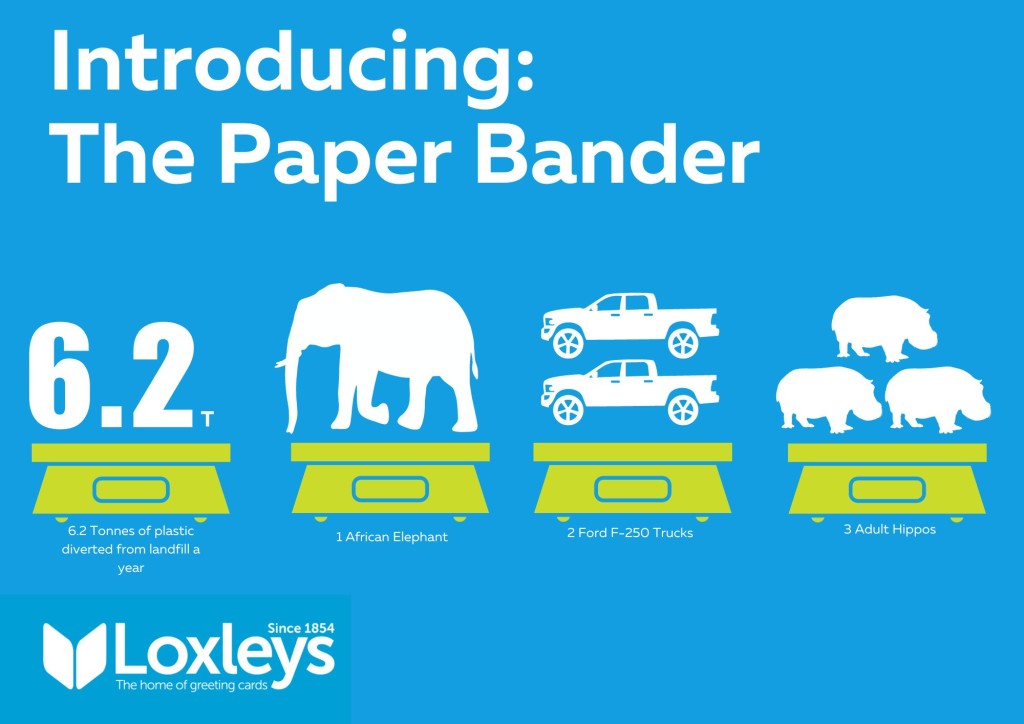
Significantly reducing landfill waste and greenhouse gas emissions, it will result in an annual saving of 6.2tonnes of plastic, equivalent to the weight of one African elephant, two Ford trucks or three adult hippos!
The machine is also capable of being adapted to run other solutions within the eco-range, allowing future development of innovative plastic-free production and packaging for greeting cards.
In other sustainability moves, Loxleys has completed a full transition to LED lighting throughout its premises, reducing on-site energy usage and decreasing carbon output by 9,316 KgCO2e., and an investment in voltage optimisation technology, which optimises incoming supply from the national grid to match the voltage required by onsite equipment, will cut energy usage by a further 7%.
The printer has also replaced the traditional method of chemically processing printing plates to use a sustainable chemical-free plate production method which eliminates hazardous waste and the use of water and chemicals from the process.